High-quality metrology for quality control in the measuring room, production, incoming goods and development.
Gear Metering Pumps & Meter Mix Dispense Machines with highest accuracy for processing liquids and pastes.
High-precision rotary stroke bearings for backlash-free linear and rotational movements for use in machine and device construction.
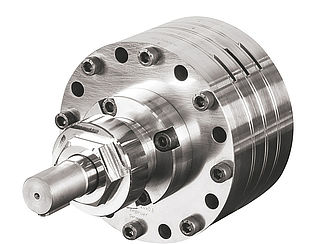
Proven use for decades to spin finest yarn: planetary spinning pumps are the heart of every synthetic fibre spinning plant.
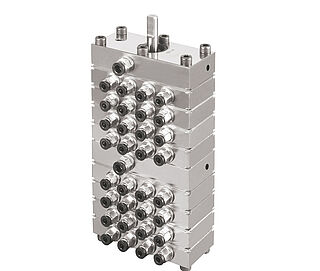
Spin finish dosing pumps do not only meter preparation fluids. They can also be used for the consistent dosing of water, perfume or even oils.
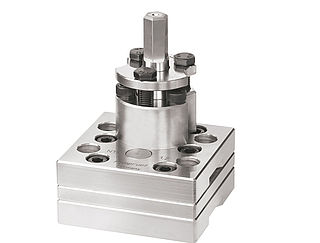
There are almost no limits to the use as a dosing pump in various industries. As a spinning pump it is only used for special applications.
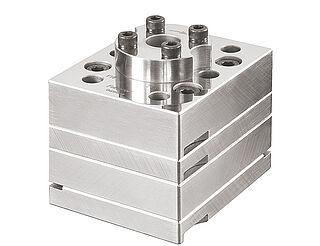
Predominantly used in spinning and adhesives technology, they offer the possibility of realizing two flow rates with minimal space and one motor drive only.
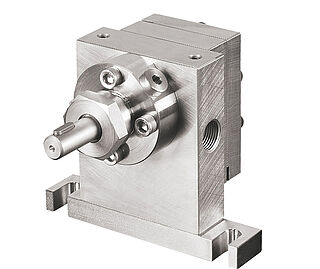
Product bores which are on both sides of the pump body allow the pump to be integrated directly into the production line.
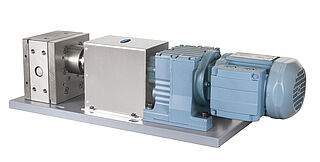
They can be used for all applications. Direct installation in the product line does not require an additional clamping block.
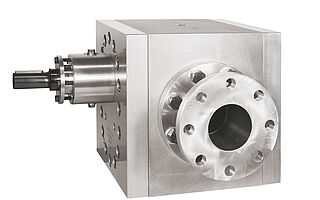
Discharge pumps ensure gentle discharge of polymer melts with low product shear. Booster pumps ensure a defined process pressure for downstream tools such as dies or extruders.
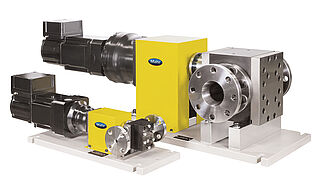
For highly accurate, low-pulsation dosing of liquids. The gear metering pumps achieve an efficient performance even at low viscosity and back pressure.

Paint metering pumps can also be used for robot applications. Even at short flushing cycles these pumps show excellent flushing results.
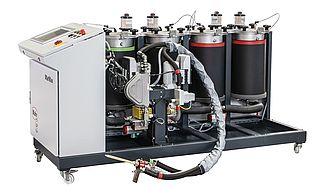
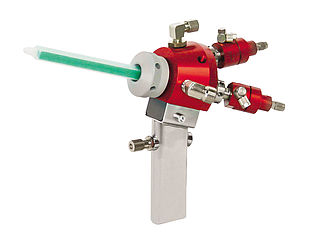
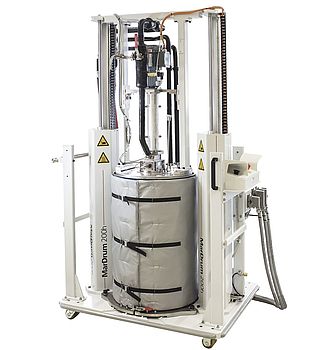
Solutions for material preparation, conditioning and supply to the meter mix dispense machine.
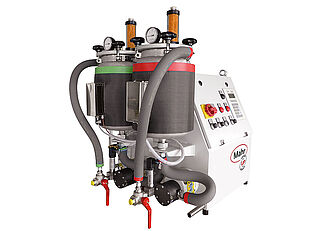
Lightweight design:
2C - 3C Meter Mix Dispense Machine for low flow rates
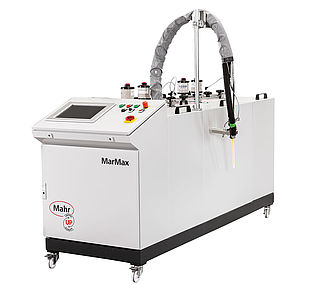
Our allrounder:
1C - 4C Meter Mix Dispense Machine for low to medium flow rates

Compact and efficient:
2C - 4C Meter Mix Dispense Machine with an output of up to 10 l/min
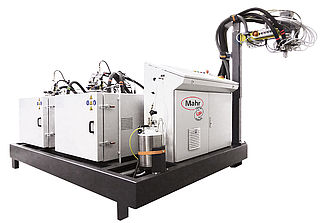
High-capacity:
2C - nC Meter Mix Dispense Machine for high material flow rates
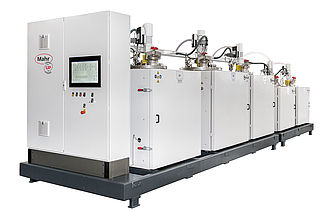
Customised solutions:
perfectly tailored to suit your application
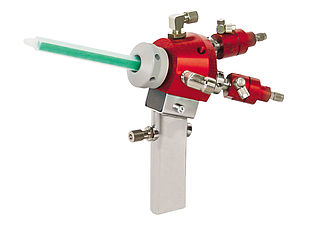
The mixing takes place exclusively through the flow movement of the components and the geometry of the mixing element.
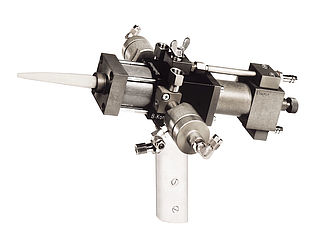
The components are mixed by a rotating element in a mixing chamber.
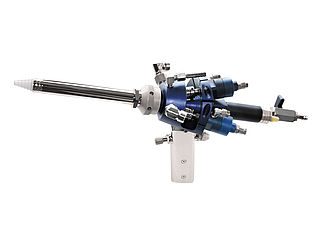
The mixing takes place through the flow movement of the components in cooperation with the geometry and rotation of the mixing element.
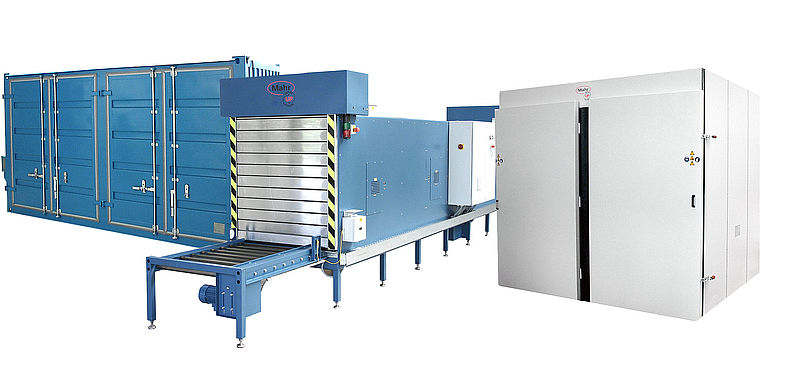
01. Tempering
For some materials it is mandatory to maintain a constant temperature in the raw material storage. In order to ensure consistent product quality, only precisely tempered drums may be used in the production process for these temperature-sensitive substances. Mahr Unipre offers various options for material temperature control, such as temperature-controlled storage facilities for external storage spaces. We will find the optimal solution for you that suits the purpose of processing and the processing quantity.
02. Material Supply – you can't do without!
Solutions for material preparation, post-processing and filling the meter mix dispense machines
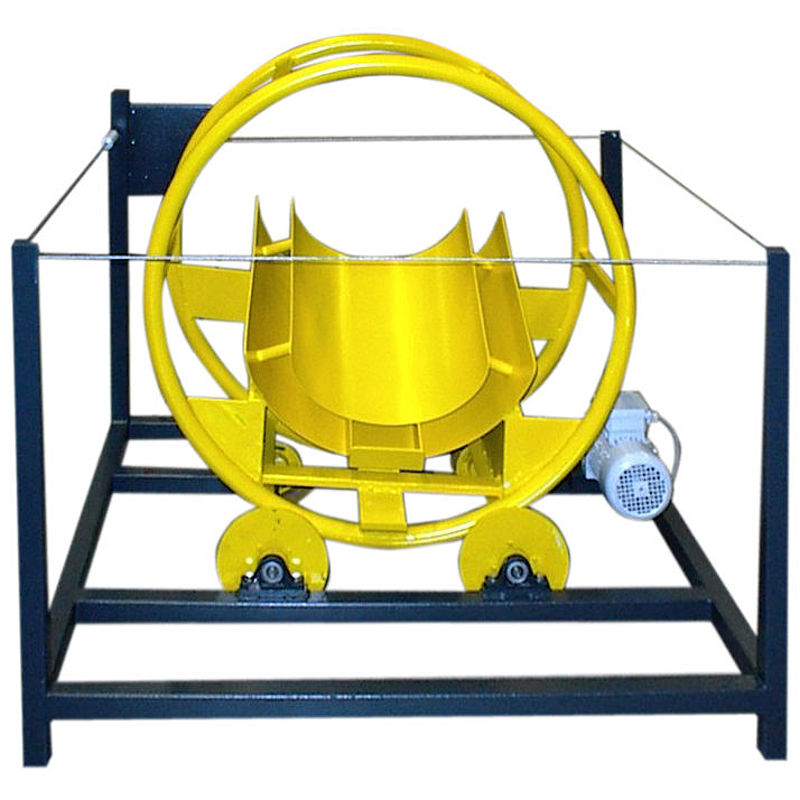
Drum Hoop Mixer
For tumbling barrels to mix deposited sediments homogeneously with the liquid.
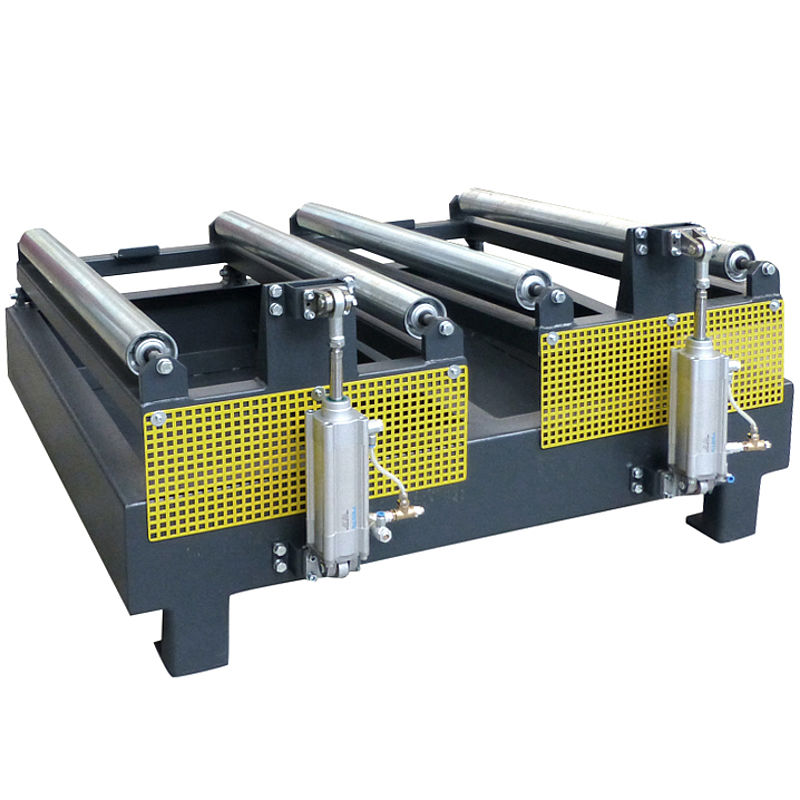
Drum Storage and Tilting Device
Horizontal storage of the drum for easy filling of the pump including tilting device for almost complete discharging.
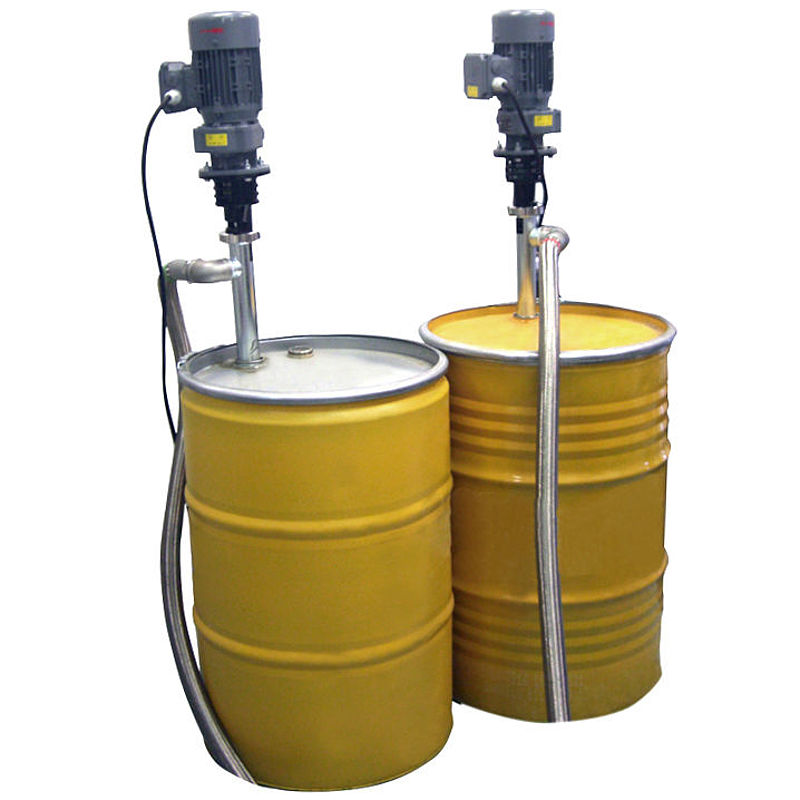
Drum Pump
Affordable device for transferring the material from the drum.
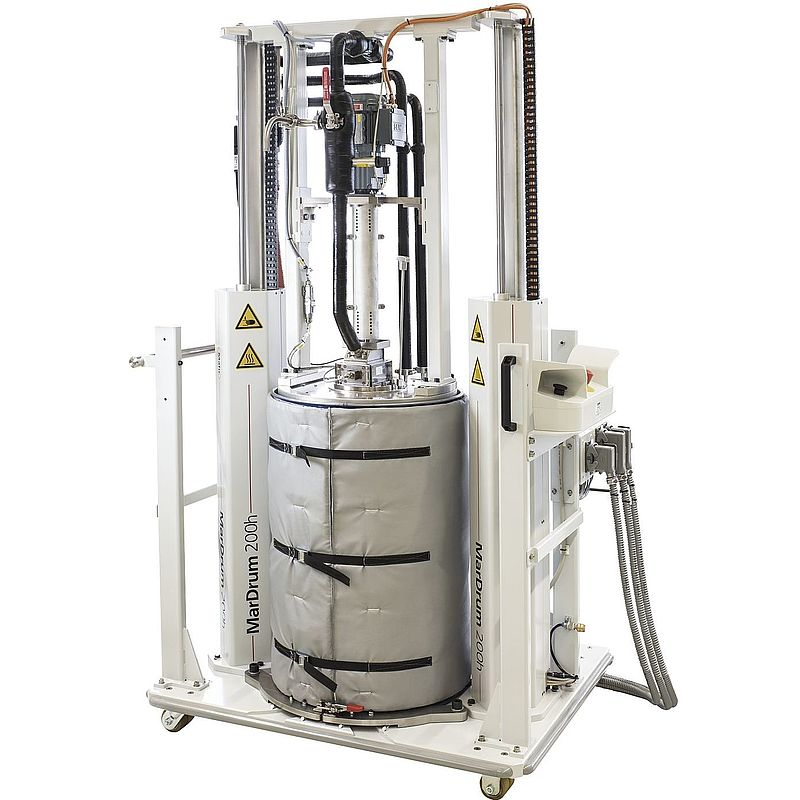
MarDrum 200h
Material discharge or dosing station with follower plate, applicable for high viscosity media.
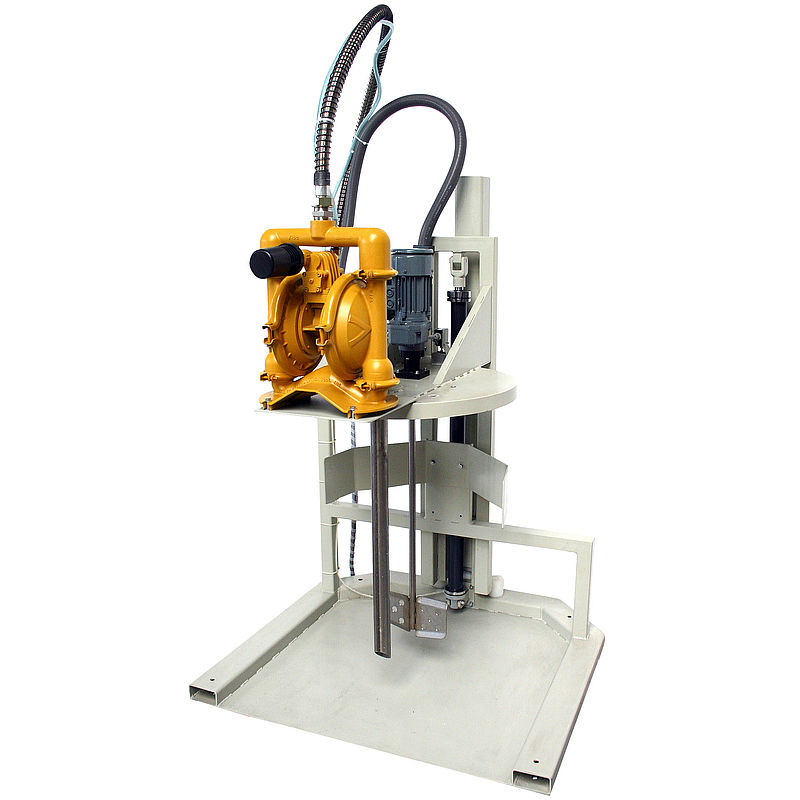
Agitating and Pumping Station
Agitating and extraction station for dispersions, e.g. to achieve a homogeneous heat distribution in the material in temperature-controlled drums.
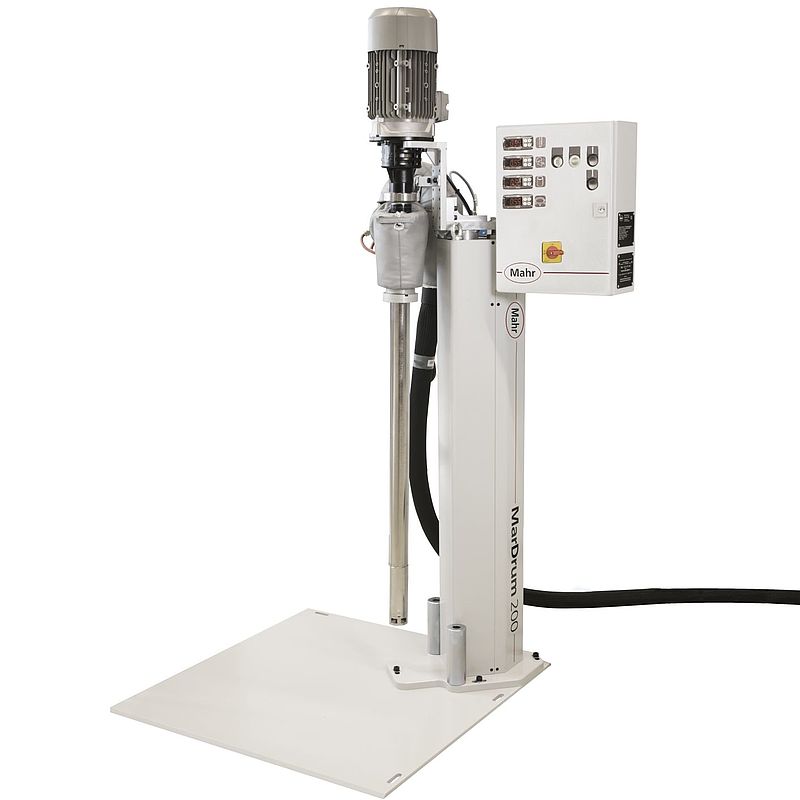
MarDrum 200
Material removal station with lifting device and connection to the dosing machine for automatic filling.
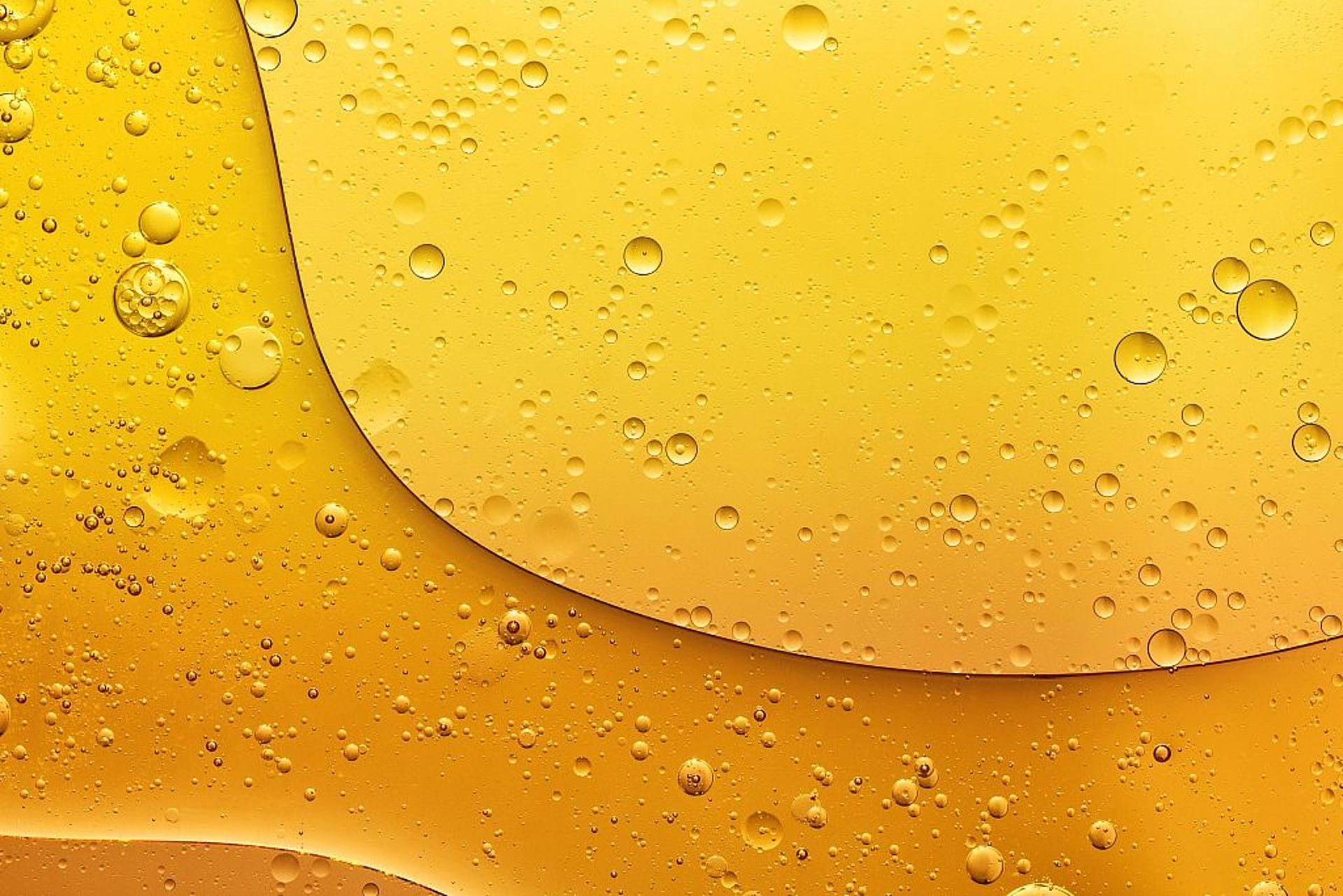
03. Dosing of Colour Additives
The color or additive is added directly at the mixing head, thus enabling the component to be changed quickly without time-consuming machine cleaning. The colour or additive components are available as separate modules for flexible connection to several compatible mixing and metering systems or integrated into the overall machine. A machine retrofit with colour or additive components is also possible in most cases. The paint, additive or additive batch tanks are available unheated, with a heating jacket or integrated in convection-heated ovens.
Suitable for these applications:
Do you have questions about our products?
Please contact us at +49 (0) 2922-87840-0