High-quality metrology for quality control in the measuring room, production, incoming goods and development.
Gear Metering Pumps & Meter Mix Dispense Machines with highest accuracy for processing liquids and pastes.
High-precision rotary stroke bearings for backlash-free linear and rotational movements for use in machine and device construction.
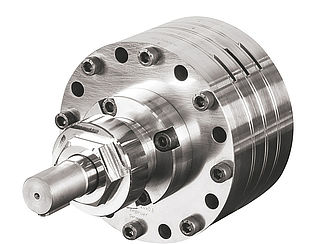
Proven use for decades to spin finest yarn: planetary spinning pumps are the heart of every synthetic fibre spinning plant.
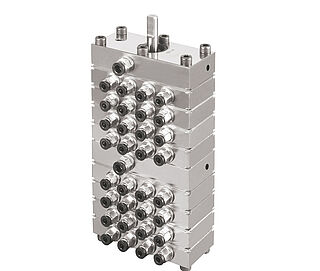
Spin finish dosing pumps do not only meter preparation fluids. They can also be used for the consistent dosing of water, perfume or even oils.
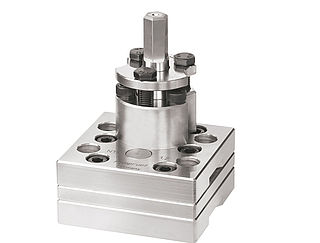
There are almost no limits to the use as a dosing pump in various industries. As a spinning pump it is only used for special applications.
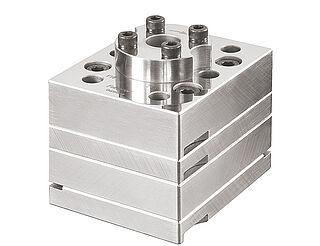
Predominantly used in spinning and adhesives technology, they offer the possibility of realizing two flow rates with minimal space and one motor drive only.
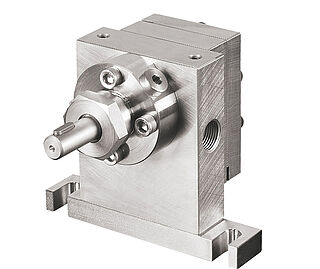
Product bores which are on both sides of the pump body allow the pump to be integrated directly into the production line.
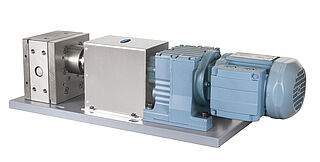
They can be used for all applications. Direct installation in the product line does not require an additional clamping block.
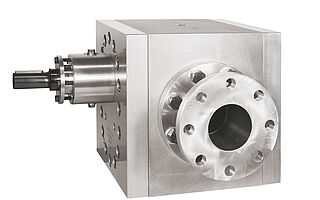
Discharge pumps ensure gentle discharge of polymer melts with low product shear. Booster pumps ensure a defined process pressure for downstream tools such as dies or extruders.
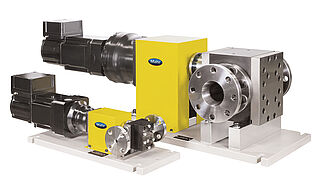
For highly accurate, low-pulsation dosing of liquids. The gear metering pumps achieve an efficient performance even at low viscosity and back pressure.

Paint metering pumps can also be used for robot applications. Even at short flushing cycles these pumps show excellent flushing results.
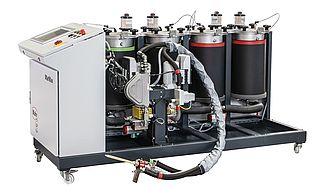
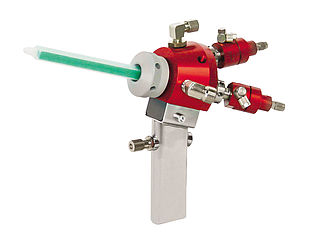
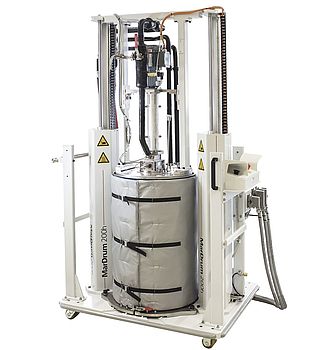
Solutions for material preparation, conditioning and supply to the meter mix dispense machine.
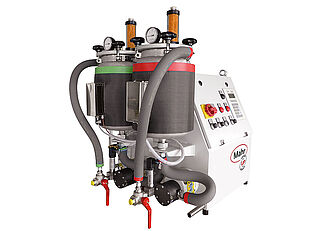
Lightweight design:
2C - 3C Meter Mix Dispense Machine for low flow rates
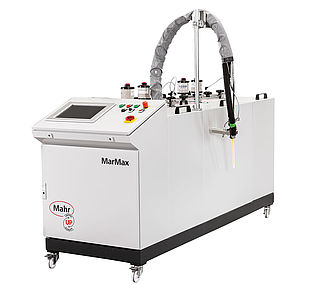
Our allrounder:
1C - 4C Meter Mix Dispense Machine for low to medium flow rates

Compact and efficient:
2C - 4C Meter Mix Dispense Machine with an output of up to 10 l/min
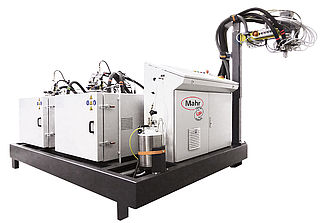
High-capacity:
2C - nC Meter Mix Dispense Machine for high material flow rates
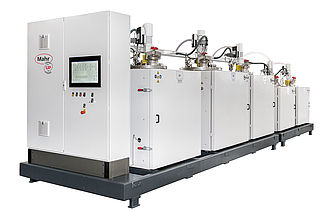
Customised solutions:
perfectly tailored to suit your application
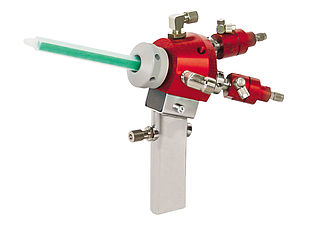
The mixing takes place exclusively through the flow movement of the components and the geometry of the mixing element.
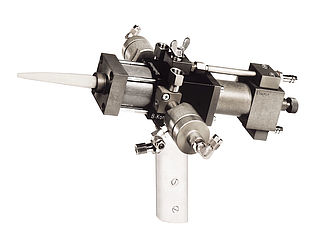
The components are mixed by a rotating element in a mixing chamber.
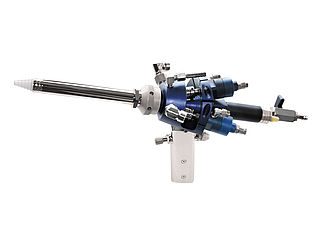
The mixing takes place through the flow movement of the components in cooperation with the geometry and rotation of the mixing element.
Gear metering pumps enable the exact dosing of polymer melts. This is particularly important in the manufacture of high-quality products. They can also take over the function of pressure increase, for example in the following processes:
- Extrusion Processes
- Continuous spinning processes
- Chip spinning processes
The advantage of using a gear metering pump to increase pressure can be explained using an example: in the extrusion process, the pump installed between the extruder and the extrusion tool takes over the process task of "pressure build-up", i.e. it builds up the melt pressure required to overcome the tool. The volumetric mode of operation of the pump guarantees constant melt volumes per time unit at constant pump speed. The extruder only takes over the plasticizing, homogenization and, if necessary, degassing of the melt. In comparison with a single-screw extruder, the pressure build-up in the gear metering pump takes place both with a higher energy efficiency and on a shorter process length, which means a considerably shorter residence time. This leads to an immediately increased product quality due to the reduced thermal load on the melt. Ultimately, the use of a pressure booster pump means particularly gentle and very efficient pumping of the polymer melt.